Sponsored by Mentor, a Siemens Business
Download the free whitepaper below
How Electromagnetics Engineering Surrounds
Us
By Prof David Lowther, McGill University, Canada; and Mentor, a Siemens Business
Have
you ever asked yourself what happens to the sensors on your car when it rains?
Probably not often, if ever. Yet this is just one of the countless and
inconspicuous ways electromagnetic engineering has revolutionized the way we
live.
Consider
these three examples which are more striking and apparent:
- Energy and Efficiency. Our modern societies function as a result of being able to create and use electromagnetic energy. The fact that energy can be transmitted between two points through the use of a flexible conducting cable has allowed manufacturing processes to be rethought and factories to be redesigned and relocated.
- Connectivity has become second nature. Consumers expect high-quality connectivity all the time. This includes fast download speeds on portable devices with lower latency and low power consumption. The same holds true for all facets of industry communications, from communication between satellites and base stations, moving cars and infrastructure and robots and production line control stations, to name a few.
- With this boom in global communication networks comes more EMI and EMC issues between communication devices, cables and electric wire harnesses. Both radiated and conducted power emissions will need more attention, and there is no doubt properly engineering these high-level requirements will be a challenge.
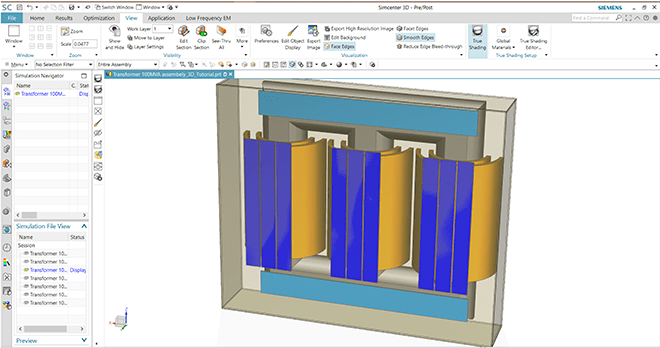
There are quite a few
factors to take into consideration for every electromagnetic puzzle throughout
the frequency range.
Electromagnetics
is not a one-size-fits-all job, experts typically categorize issues according
to whether the electromagnetic field changes are radiated or not. This gives
rise to two categories often referred to as high or low frequency
electromagnetic problems. Each one has its own typical characteristics and
methodology.
All electromagnetic
devices have something in common: complexity. They typically require complex
shapes to define the desired field structure. The materials used often behave
in a non-linear fashion (for example, the relationship between magnetic fields
and magnetic fluxes are variable). The field wavelength is much larger than the
overall device dimensions. (for example, a one megahertz (MHz) wavelength in
free space is about 300 meters so any device with a few centimeters as its
maximum dimension will have negligible radiation).
Another major challenge
that experts tend to take for granted is scale. Unlike many other areas of
physics, the range of scale in a device is huge. As an example, for a
transformer you must consider components that are submillimeter in size in a
device in which overall dimensions are measured in tens of meters.
This is a scale factor of
at least 10,000 to 1. In certain aerospace applications, you have features that
are submillimeter in a structure, which is tens of meters in size. How do you
handle issues of scalability in both low-frequency and high-frequency
scenarios?
From
Industry 4.0 automotive and aerospace manufacturing to heavy equipment, innovative
electric motor design and development have become industry make or breaks. Not
only are high performance, sustainability and efficiency at the top of the
list, significant drivers like the cost of materials, manufacturing and
operation are also vital factors in the design and development process. For
electromagnetics, accurately representing material behavior and related local
loss determinations will help predict machine behavior from a design point of
view.
A good example is the traction drive. Engineers have been looking at the use of synchronous reluctance motors to significantly reduce manufacturing costs by removing the expensive permanent magnets (often neodymium magnets). This can lead to a significant loss of torque for certain frame sizes. To overcome this, relatively cheap permanent magnets (alnicos or ferrites) can be used within the flux barriers to increase the torque of the machine without significantly increasing costs.
Both automotive and aerospace industries already have regulations for dealing with EMI/EMC issues and electromagnetic shielding is a quite common domain with a wide range of applications. But with the arrival of highly complex products and large-scale EV powertrains in transportation and heavy equipment, there are some areas that still need investigation. In the next section we will look at what the aerospace industry is doing with EMI/EMC and how digital twins can help during the design phase and provide support during certification.
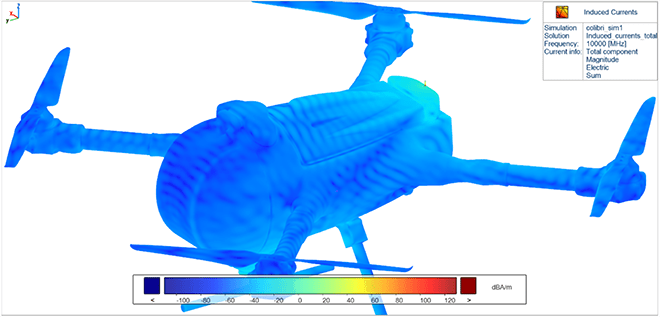
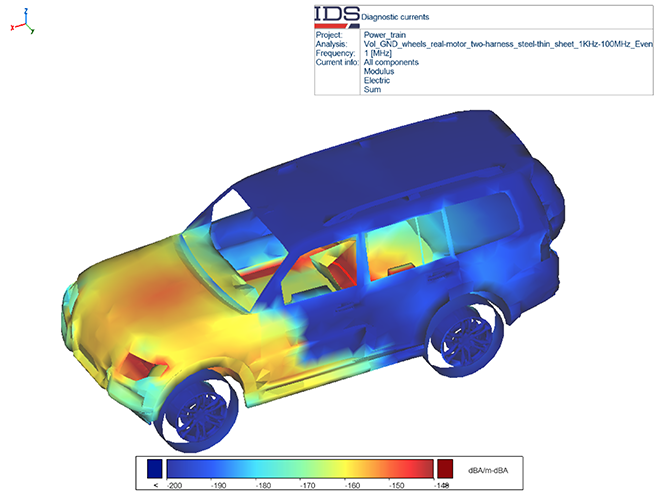
There
is a clear need for a broad, multifunctional toolset for electromagnetic
engineering that can seamlessly link design and analysis digital twins
throughout the development cycle. Once validated, these digital twins live on
in PLM ecosystems and mobility chains, facilitating seamless product updates
and autonomous driving data base enhancements.
By using such a toolset, engineers can not only obtain a more optimal solution, but they can gain precious time compared to current processes. Taking a holistic approach with a multifunctional and a broad toolset facilitates the seamless integration of electromagnetic applications into the overall design and development process. This results in more efficient, sustainable and better optimized products from complex airplanes and self-driving automobiles to connected consumer goods.
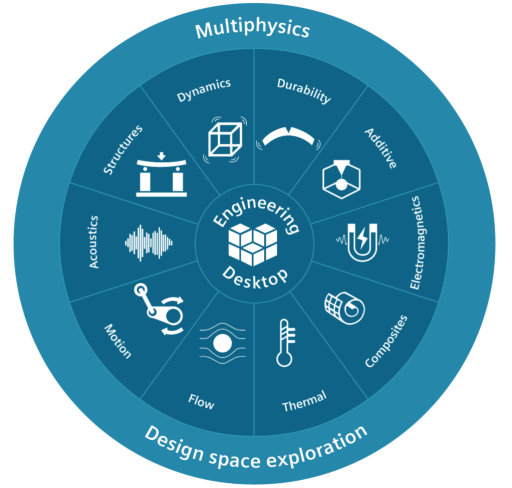
Simcenter™
3D v19.2 has newly integrated electromagnetic simulations so that engineering
teams can work in closer collaboration to address these challenges .The Electromagnetics
modules include a low frequency solver from Simcenter MAGNET and a
high-frequency solver for wave propagation class of problems.
This augments the existing toolset for electromagnetic engineering: Simcenter SPEED & Simcenter Motorsolve which are uniquely for electric motor design and the specialized Simcenter Star-CCM CFD-EM simulations.
Download the free whitepaper
Treating permanent magnets as linear materials is a simpler numerical implementation, especially if there is a lack of measured data. However the BH curves of permanent magnets such as NeFeB exhibit two almost linear sections joined by a sharp curve known as a knee point in the second quadrant of the BH plane. Once the operating point moves past the knee point, the magnet is no longer considered good because it has lost its magnetization. Is there a computationally efficient way to properly incorporate a demagnetization model, a necessity for the e-powertrain motors which face extreme operating conditions including high currents and temperatures which can lead to partial or complete demagnetization?