German electronic 3D printing company Neotech AMT is embarking upon a joint project with the TAMS-group at the University of Hamburg to develop an Artificial Intelligence (AI) driven Quality Assurance (QA) system for 3D printed electronics.
Funded by the Central Innovation Program for SMEs (ZIM), deployed by the German Federal Ministry for Economic Affairs and Energy (BMWi), the project aims to pave the way for closed-loop control for hybrid manufacturing processes and will run until September 2022.
“This exciting development opens the way for guaranteed QA and traceability in ‘fully additive’ 3D printed electronics while also increasing product yields,” said Martin Hedges, managing director of Neotech AMT. “The risk of defects only being discovered after lengthy manufacturing processes is mitigated and autocorrection will bring yield losses to an absolute minimum.”
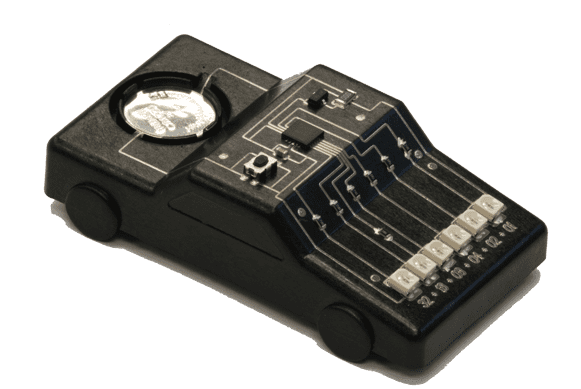
The QA system
The system developed by Neotech and the TAMS-group is camera-based and will facilitate the online monitoring of manufacturing processes in a 5-axis manufacturing cell, enabling automated QA. To achieve this, the system will record and classify the manufacturing process in order to automatically correct processing errors.
A camera-based vision system will record and compile images of printed electrical structures in 3D space, which can be recognized by image processing using AI. During this phase, the AI-powered technology checks for potential defects within the electrical device, such as geometrical errors, short circuits, and line breaks. If a defect is detected, the system will deploy one of three options, namely automated correction, correction with operator input, or part rejection. This feedback creates a closed-loop printing process where automated QA can be achieved.
The data generated throughout the process can then be archived for documentation for the support of certification processes within critical applications.
“This project is an important step towards closed-loop control for hybrid manufacturing processes,” said Florens Wasserfall of the University of Hamburg. “Variations in quality and accuracy have been a major limitation ever since the invention of additive technologies.
“Active process monitoring is a core aspect to enable reliable and scalable manufacturing of highly integrated, smart products.”
Neotech AMT and 3D printed electronics
Neotech has previously engaged in several projects to advance additive manufacturing. One of these, known as ‘Hyb-Man’, brought together 11 partner groups from Germany and the Netherlands to develop hybrid manufacturing techniques involving 3D printed polymers as well as 3D printed electronics. While another, named AMPECS, focused on the printing of ceramic substrates as a compliment to electronics 3D printing.
Last year, Neotech presented its “Fully Additive” 3D printed electronics at RapidTec. “Fully Additive” refers to a combination of 3D printed electronics with traditional 3D printing and 3D Pick & Place of Surface Mount Devices. These smart devices contain electronics functionality, both externally and also embedded within the 3D printed body.
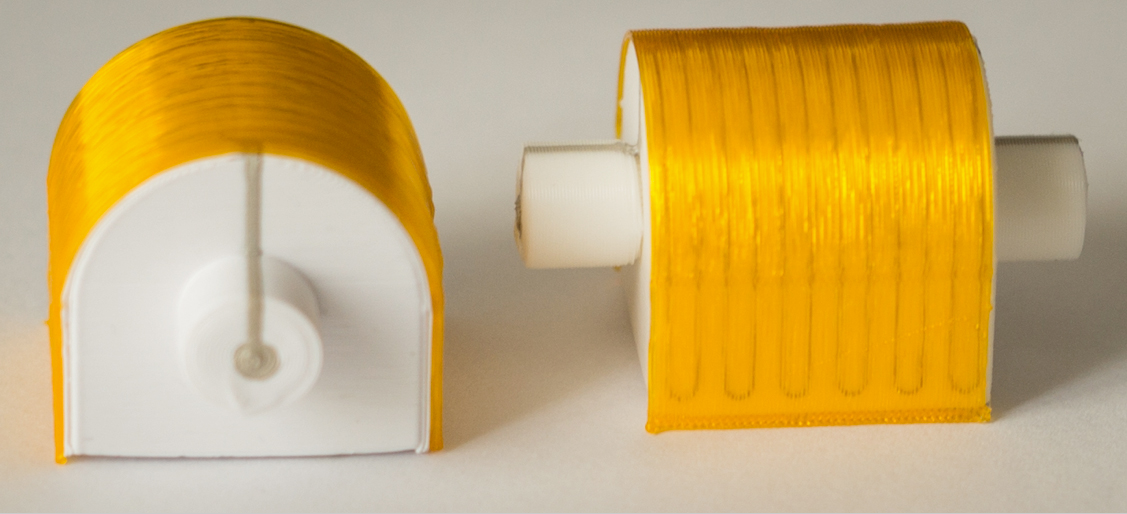
Developments in QA
According to Gregor Reischle and Christophe Blanc of global certification firm TÜV SÜD, comprehensive QA is “an imperative factor” in achieving serial production based on additive methods. Several companies have forged recent developments in QA not only to meet the requirements of serial production but also to minimize waste material from misprints and gain time savings.
At the beginning of last year, Sigma Labs, a computer-aided inspection (CAI) software company, became a member of the UK’s Manufacturing Technology Centre (MTC) to enable in-process quality monitoring for additive manufacturing systems at the MTC’s National Centre for Additive Manufacturing, through its PrintRite3D INSPECT In-Process Quality Assurance (IPQA) software. A few months later, Sigma Labs signed a Memorandum of Understanding (MoU) with Belgian 3D printing software company Materialise for the development of an integrated in-situ quality assurance (QA) system for metal 3D printing.
More recently, Sigma Labs announced a new edition of its PrintRite3D quality assurance software in April, known as the Production Series, alongside two U.S. patents for its PrintRite3D software.
Elsewhere, researchers from the Swanson School of Engineering received over $1 million to produce a quality assurance method for the additive manufacturing of new-generation gas turbine components, while VELO3D released its Assure Quality Assurance and Control System for its laser powder bed fusion (LPBF) Sapphire 3D printers. On-demand 3D printing service Stratasys Direct Manufacturing was the first to implement and validate the system in November last year.
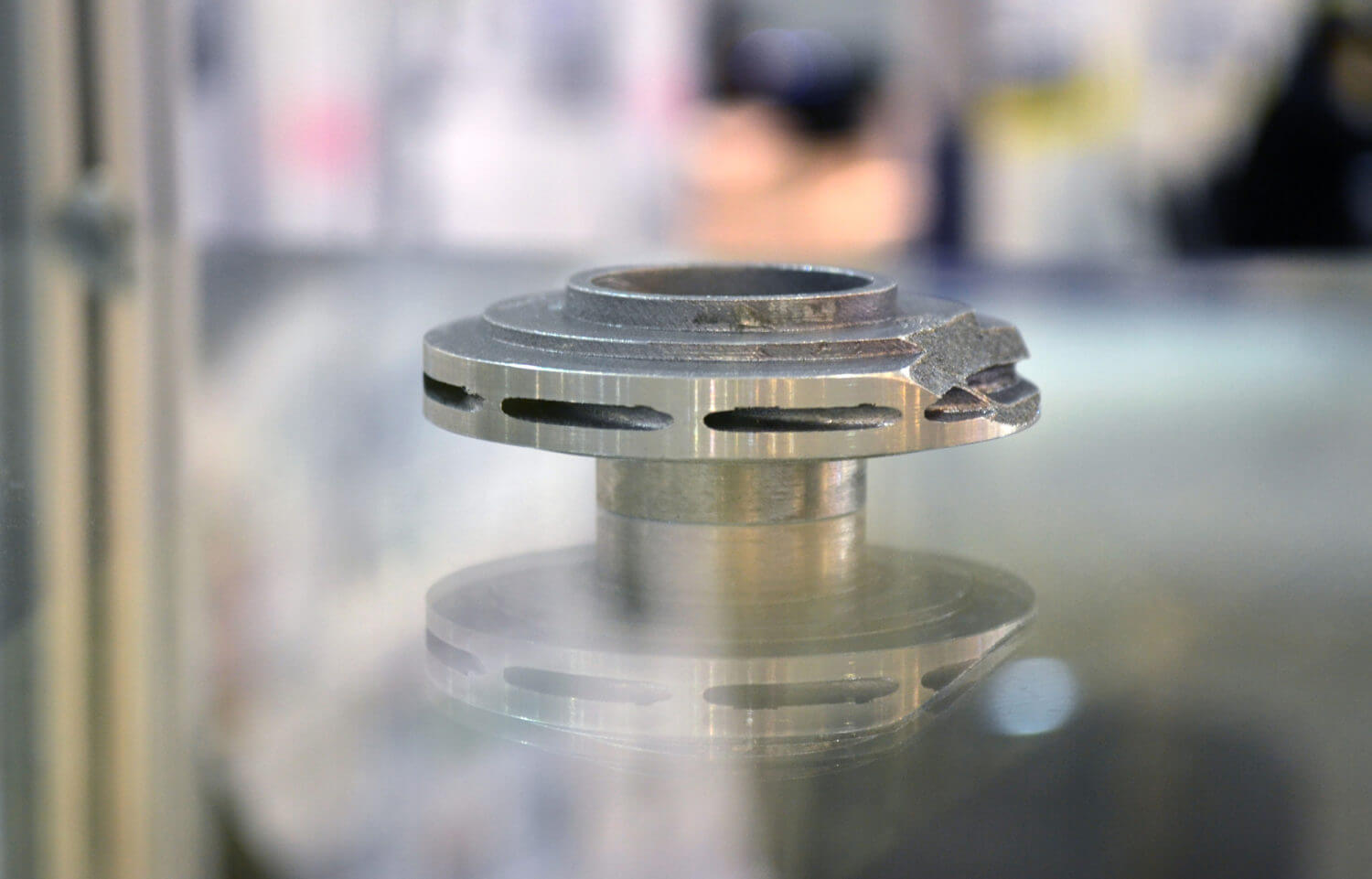
Subscribe to the 3D Printing Industry newsletter for the latest news in additive manufacturing. You can also stay connected by following us on Twitter and liking us on Facebook.
Be sure to subscribe to the Another Dimension podcast on your chosen podcast player to make sure you never miss an episode.
Looking for a career in additive manufacturing? Visit 3D Printing Jobs for a selection of roles in the industry.
Featured image shows 3D MID Sensor Circuit. Filling level sensor constructed from Ag on PA6 with added SMDs. Image via Neotech AMT.